Глава 8. Оборудование для транспортировки изделий
- 8.1. Ручные однорельсовые конвейеры
- 8.2. Конвейеры с непрерывным движением цепи
- 8.3. Свободно-приводные конвейеры
- 8.4. Напольные конвейеры
- 8.5. Выбор транспортных средств
- 8.6. Эксплуатация и техническое обслуживание конвейеров
- 8.7. Безопасность и методы управления
Существует много методов транспортировки деталей, удовлетворяющих потребности промышленного производства. В данной главе описаны промышленные, стандартные методы, выдержавшие испытание временем. Фактически многие из них были первоначально разработаны еще в первой половине двадцатого века.
Транспортировка изделий необходима для всех систем нанесения покрытий. Даже в производствах, выпускающих продукцию мелкими партиями, требуются тележки или рельсы для транспортировки деталей от одного этапа обработки к другому. Система транспортировки деталей, или конвейер, является средством, при помощи которого изделия переносятся через участки очистки, нанесения покрытия и термообработки в системе нанесения покрытий. Конвейер может также служить своеобразным хранилищем обрабатываемых деталей при их нахождении на производственном участке.
Конвейерная система может транспортировать детали любого типа, размеров и конфигурации, начиная от канцелярской скрепки и кончая кузовом автомобиля.
Варианты конвейеров на участках нанесения покрытий разнообразны. Они включают относительно простые ручные однорельсовые конвейеры типа "тяни-толкай", а также полностью автоматизированные свободно-приводные конвейерные системы. Можно выбрать конвейер, соответствующий требованиям к производительности, уровню автоматизации, занимаемой площади и простоте обслуживания. Кроме того, эти варианты дают возможность снизить требуемые капиталовложения до желаемого уровня.
Простейший метод транспортировки деталей - ручная система типа "тяни-толкай" - лучше всего подходит для малых объемов производства с простыми потребностями производственного процесса. Это, по существу, самый дешевый метод транспортировки.
Чаще всего при нанесении покрытий используются недорогие подвесные цепные и напольные конвейеры.
Наиболее гибким и сложным средством транспортировки является свободно-приводной конвейер. Этот метод позволяет отдельным деталям останавливаться либо замедлять ход, тогда как остальная часть конвейера продолжает двигаться. Свободно-приводной конвейер может быть также сконструирован с многочисленными выступами, облегчающими загрузку или выгрузку деталей, оперативную обработку, удовлетворяющую требованиям производств. Кроме того, конструкция такого конвейера может предусматривать накопление, хранение и распределение деталей. Свободно-приводной конвейер является удобным гибким средством переноса изделий при нанесении покрытий на участках с производительностью, составляющей сотни операций в час. Однако вся эта гибкость конструкции и пропускная способность достигаются за счет значительного повышения цены, что делает такой метод транспортировки деталей весьма дорогостоящим.
8.1. Ручные однорельсовые конвейеры
Самая распространенная конвейерная система представляет собой подвесной конвейер, приводимый в действие оператором и состоящий из однорельсового пути для тележек. По этому пути движутся тележки, перевозящие погруженные на них детали. Как показано на рис. 8.1, ручная конвейерная система типа "тяни-толкай" может представлять собой систему с закрытой дорожкой либо систему с двутавровой балкой.
Конвейеры "тяни-толкай" с закрытой дорожкой самого легкого режима обычно имеют отдельные тележки грузоподъемностью 100 кг. Комбинируя несколько тележек с использованием нагрузочного рычага, можно увеличить грузоподъемность примерно до 400 кг. Более тяжелый конвейер может быть построен с применением двутавровой балки размерами от 75 до 380 мм (от 3 до 15 дюймов). В зависимости от загрузки деталями отдельные тележки могут иметь грузоподъемность от 80 до 1600 кг.
Перемещение изделий осуществляется операторами, которые вручную толкают или тянут их от одной позиции к другой, вперед или назад. Поскольку оператор вручную толкает груз по дорожке, все рельсы конвейеров должны располагаться строго горизонтально.
Ручные системы "тяни-толкай" могут оснащаться приспособлениями для поворотов в горизонтальной плоскости и переключателями дорожек, как показано на рис. 8.2. Возможность переключения дорожек позволяет операторам двигать детали на отдельные участки для выполнения различных операций. Ручная система "тяни-толкай" может иметь упоры для неподвижного закрепления тележек на время выполнения операции.
Рис. 8.1. Ручные конвейеры с закрытой дорожкой (а) и с двутавровой балкой (в):
1 - трек; 2 - тележка; 3 - нагрузочный рычаг
Рис. 8.2. Типовой маршрут ручного однорельсового конвейера (вид сверху):
1 - распылительная камера; 2 - деталь; 3 - переключатель дорожек;
4 - погрузка/разгрузка; 5- установка для подготовки поверхности; 6- печь
Рис. 8.3. Транспортировка деталей на конвейере
при прямой (а) и косой (б) ориентации (вид сверху):
1 — деталь; 2 - переключатель входа на дорожку;
3 - переключатель выхода с дорожки
Вследствие зависимости ручной системы "тяни-толкай" от обслуживания рабочими она обычно применяется только для малых объемов производства.
Ручные системы "тяни-толкай" привлекают тех пользователей, которые могут примириться с их малой производительностью. В этих системах используются стандартные узлы конвейеров, которые обычно имеются на складах в готовом виде. Длинные изделия можно перемещать косой или тандемной ориентацией (рис. 8.3), благодаря чему уменьшается занимаемая площадь. Ручные системы "тяни-толкай" характеризуются низкой производительностью и пригодны только для простых операций, но обычно они компактны и уход за ними минимален, поскольку движущимися частями являются только тележки, которые катятся по неподвижным дорожкам, а также переключатели дорожек, если они используются. Ручная конвейерная система "тяни-толкай" не требует никакого управления, поскольку любые переключатели дорожек могут приводиться в действие вручную.
Одним из основных недостатков конвейерных систем "тяни-толкай" является их зависимость от персонала, занятого на перемещении изделий. Поскольку получение покрытий связано с несколькими операциями, такими, как подготовка поверхности, нанесение порошка и термообработка, ручная система "тяни-толкай" может быть использована только для малых партий изделий. Никакая непрерывная обработка не представляется возможной. Необходимо соблюдать большую осторожность при перемещении изделий со свежим покрытием от камеры нанесения порошка к печи термообработки, чтобы исключить возникновение дефектов покрытия. Ориентировочное усилие, требуемое от оператора для перемещения груза, подвешенного к хорошо смазанным тележкам ручной системы "тяни-толкай", составляет приблизительно 2,5 % от его веса.
8.2. Конвейеры с непрерывным движением цепи
Первым шагом к усложнению ручных однорельсовых конвейерных систем явился конвейер с непрерывным движением по закрытой дорожке (рис. 8.4). Эта одинарная подвесная дорожка имеет непрерывно движущуюся цепь, заключенную внутри нее. Нагрузку несут вертикальные колеса, горизонтально ориентированные направляющие колеса помогают цепи огибать углы при поворотах в горизонтальной плоскости.
Устройство привода обеспечивает непрерывное движение бесконечной цепи, транспортирующей детали. Конвейер с непрерывным движением цепи по закрытой дорожке может представлять собой часть полной системы с приспособлениями для поворотов в горизонтальной плоскости и изменения высоты по кривым в вертикальной плоскости, как это показано в качестве типичного примера на рис. 8.5. Однако никакие переключения не представляются возможными, поскольку все детали переносятся одной цепью, технологические процессы во всей системе осуществляются с одной скоростью. Ни одна из отдельных деталей не может быть остановлена на конвейере с непрерывным движением цепи, поскольку конвейерная цепь может либо непрерывно двигаться, либо останавливаться только полностью. В некоторых системах рабочую скорость конвейера можно изменять.
Рис. 8.4. Конвейер с непрерывным движением цепи по закрытой дорожке:
1 - формованная секция закрытой дорожки; 2 - вертикальные колеса, несущие нагрузку;
3 -горизонтальные направляющие колеса; 4 - отдельное жесткое крепление;
5 - крепление нагрузочного рычага; 6- конвейерная цепь
Конвейер с непрерывным движением цепи по закрытой дорожке наилучшим образом подходит для больших объемов производства с непрерывным, но умеренным потоком деталей малого веса. Для процессов нанесения покрытий часто характерен такой режим работы.
Одно из преимуществ конвейера с непрерывным движением цепи по закрытой дорожке - его низкая стоимость, поскольку вся система может быть собрана из легкодоступных узлов стандартных размеров. Кроме того, эти конвейеры просты в эксплуатации, так как необходимо обслуживать только цепь, привод и подъемник. Никаких специальных механизмов, помогающих цепи огибать углы при поворотах в горизонтальной плоскости или менять высоту, не требуется.
Рис. 8.5.
Компановка оборудования при использовании конвейера
с непрерывным движением цепи по закрытой дорожке (вид сверху):
1- участок загрузки; 2 - агрегат подготовки поверхности;
3 - сушильная камера; 4 - помещение для нанесения покрытия;
5 - камера для нанесения порошка в рабочем положении;
6- камера для нанесения порошка (сменная) в нерабочем положении;
7- печь для отверждения покрытия; 8 - охлаждение;
9- участок разгрузки
Закрытая конфигурация дорожки (кожух закрывает большую часть конвейера) помогает защитить конвейерную цепь от загрязнения. Это также сводит к минимуму возможность попадания загрязнения с конвейерной цепи на изделия, что, в свою очередь, уменьшает потребность в санитарных поддонах. Закрытая дорожка может быть перевернута таким образом, что ее щель будет обращена вверх, при этом используются специальные крюки и крепления. В этом случае попадание загрязнений с конвейерной цепи на изделие почти невозможно. Цепи, движущиеся по закрытой дорожке, могут совершать повороты меньшего радиуса в горизонтальной плоскости по сравнению с цепями, движущимися по двутавровой балке. Это обеспечивает более компактную компоновку оборудования. Для включения и выключения конвейеров с непрерывным движением используются самые простые органы управления.
Конвейер с закрытой дорожкой непригоден для средних или больших нагрузок. Он не дает возможности переключения маршрута движения деталей или их обработки с различными скоростями. Кроме того, для такого конвейера ограничена максимальная длина. При использовании одного приводного механизма она составляет приблизительно 300 м. Фактическая максимальная длина, указываемая поставщиком конвейера, определяется, в частности, нагрузкой от транспортируемых изделий, мощностью привода и тяговым усилием, необходимым для перемещения цепи.
Конвейеры с непрерывным движением цепи по двутавровой балке (рис. 8.6) имеют много отличий от конвейеров с непрерывным движением цепи с закрытой дорожкой. Используют двутавровые балки разных размеров. Некоторые фирмы изготавливают дорожки двутавровых балок из высокоуглеродистой стали для повышения прочности секций. Тележки, свешивающиеся с двутавровой балки, поддерживают как деталь, так и бесконечную конвейерную цепь без заклепок, которая соединяет между собой все тележки. Открытые тележки перемещаются по нижней полке двутавровой балки.
Существуют различные приспособления для поддерживания деталей. Эти приспособления прикрепляются болтами к тележкам на расстоянии, соответствующем удвоенному размеру двутавровой балки. Это расстояние является также шагом цепи.
Грузоподъемность тележек для двутавровых балок составляет:
Ширина балки, дюйм (мм) |
Грузоподъемность, кг |
---|---|
2 (50,8) |
40 |
3 (76,2) |
80 |
4(101,6) |
160 |
6 (152,4) |
480 |
Привод обеспечивает непрерывное движение замкнутой цепи, необходимое для транспортировки детали. Как и конвейер с закрытой дорожкой, конвейер с двутавровой балкой может работать как полная система с поворотами в горизонтальной плоскости и возможностью изменения высоты по кривым в вертикальной плоскости (см. рис. 8.5). Как и для конвейера с закрытой дорожкой, никакие переключения при использовании системы
Рис. 8.6. Приводной конвейер с непрерывным движением цепи по двутавровой балке:
1 - дорожка двутавровой балки; 2 - тележка; 3 - конвейерная цепь без заклепок;
4 - крепление нагрузочного рычага
Рис. 8.7. Типичная конфигурация санитарного крюка и поддона:
1 - дорожка конвейера; 2 - подвеска санитарного поддона; 3 - тележка;
4 - конвейерная цепь; 5 - С-образный санитарный крюк;
6- санитарный поддон; 7- нагрузка от изделий
с непрерывным движением цепи не представляются возможными. Поскольку все детали переносятся одной цепью, технологические процессы во всей системе осуществляются с одной скоростью. Ни одна из отдельных деталей не может быть остановлена на конвейере с непрерывным движением цепи, поскольку конвейерная цепь может либо непрерывно двигаться, либо останавливаться только полностью. В некоторых системах возможно изменение рабочей скорости конвейера.
Конвейер с непрерывным движением цепи по двутавровой балке идеально подходит для больших объемов производства с непрерывным, но умеренным потоком деталей как малого, так и большого веса. Часто такой режим работы характерен для систем нанесения покрытий из порошковых красок.
Если попадание грязи с двутавровой балки, колес тележек и цепи на изделия вызывает озабоченность, можно установить санитарные крюки для каждой из тележек, переносящих груз. Такой крюк охватывает санитарный поддон, закрепляемый непосредственно под конвейерной цепью, как показано на рис. 8.7.
Как и конвейер с закрытой дорожкой, конвейер с непрерывным движением цепи может легко преодолевать изменения высоты в вертикальной плоскости, давая возможность хранения и обработки деталей на большей высоте. Для их включения и выключения также используются самые простые органы управления.
Конвейер с непрерывным движением цепи по двутавровой балке не дает возможности переключения маршрута обработки деталей или их обработки с различными скоростями. Другим ограничением, налагаемым на конвейер с непрерывным движением цепи по закрытой дорожке, является максимальная длина. При использовании одного приводного механизма эта длина составляет приблизительно от 300 до 600 м.
8.3. Свободно-приводные конвейеры
Наиболее сложными подвесными конвейерами для транспортировки деталей являются свободно-приводные системы. Свободно-приводной конвейер состоит из "дорожки с приводом" и "свободной" дорожки. Дорожка с приводом также имеет непрерывно движущуюся цепь, как и описанные выше конвейеры. По свободной дорожке перемещаются тележки, несущие нагрузку. Дорожка с приводом может располагаться как над свободной дорожкой, так и под ней. Свободно-приводные конвейеры могут иметь разные конфигурации: с закрытой дорожкой (бесконечная цепь движется по закрытой дорожке, рис. 8.8), с двутавровой балкой (бесконечная цепь движется по двутавровой балке, рис. 8.8 и 8.9). Цепь, движущаяся по приводному рельсу, может автоматически зацеплять и отпускать тележки на свободном рельсе своим толкателем.
Тележки свободной дорожки обычно соединяются между собой нагрузочным рычагом.
Соединение двух - четырех тележек образует люльку. Свободные тележки имеют грузоподъемность от 100 до 300 кг для рельсов свободно-приводного контейнера с закрытой дорожкой. Самые маленькие тележки двутавровых балок предназначены для 3-дюймовых каналов свободных дорожек и имеют грузоподъемность 300 кг, а самые крупные - для 6-дюймовых каналов - более 2000 кг.
Рис. 8.8. Свободно-приводной конвейер с закрытой дорожкой:
1 - крепление скобы толкателя к цепи;
2 - конвейерная цепь, движущаяся по закрытой дорожке;
3 - приводной рельс закрытой дорожки; 4 - хомут; 5 - головная свободная тележка;
6- поворотный шкворень; 7 - нагрузочный рычаг люльки;
8 - свободная хвостовая дорожка; 9- свободный рельс
Конструкция свободно-приводной системы обычно состоит из нескольких непрерывно движущихся цепей, каждая из которых имеет собственный приводной механизм. Свободно-приводные конвейеры могут конструироваться как полные универсальные системы с приспособлениями для поворотов в горизонтальной плоскости и изменения высоты по кривым в вертикальной плоскости, переключателями дорожек и упорами для люлек, транспортирующих детали (рис. 8.10). Длинные детали можно перемещать с более эффективной косой ориентацией (см. рис. 8.3) для многих процессов, благодаря чему уменьшается потребность в площади для хранения деталей или размещения оборудования.
Рис. 8.9. Свободно-приводной конвейер с двутавровой балкой:
1 - жесткая скоба толкателя бокового звена цепи; 2 - хомут; 3 - конвейерная цепь и тележки;
4 - приводной рельс двутавровой балки; 5 - поворотный шкворень; 6 - свободный рельс; 7 - головная свободная тележка;
8 - нагрузочный рычаг люльки; 9 - свободная хвостовая тележка
Поскольку свободно-приводные системы могут перемещать длинные детали, как с прямой, так и с косой или даже поперечной ориентацией, когда длинная деталь перемещается перпендикулярно двум рельсам - с приводом и без привода, такой конвейер является наиболее эффективным при работе с деталями, длина которых превышает 6 м. Детали длиной до 18 м легко переносятся свободно-приводной конвейерной системой. Так как свободно-приводная система состоит из нескольких цепей дорожек, нет никакого ограничения длины пути перемещения деталей конвейером. Крупные свободно-приводные системы могут иметь длину пути перемещения деталей до нескольких миль. Поскольку в таких системах используются несколько цепей, детали могут обрабатываться с различной скоростью, которая может быть оптимизирована для каждого этапа операции отделки (подготовки поверхности, нанесения покрытия и термообработки). Возможность перемещения люлек с деталями с разной скоростью через различные зоны системы способствует оптимальной организации производственного цикла, что, в свою очередь, позволяет использовать оборудование меньших размеров и, таким образом, уменьшить стоимость процесса.
Рис. 8.10. Типовой транспортный путь свободно-приводного конвейера (вид сверху):
1 - дробеструйная обработка; 2 - предварительная обработка; 3 - сушильная печь;
4 - участок автоматизированной загрузки № 3; 5 - участок повторной обработки;
6,7 - накопление запаса перед нанесением покрытия; 8 - обработка с косой ориентацией;
9 - помещение для нанесения покрытия; 10- кабина нанесения порошка № 1;
11 - кабина нанесения порошка № 2; 12 - кабина нанесения порошка № 3;
13 - участок загрузки № 2; 14 - устройство для длительной термообработки;
15- участок нанесения альтернативного покрытия;
16- печь термообработки участка нанесения альтернативного покрытия;
17 - участок загрузки № 1; 18 - сушильная печь;
19 - охлаждение; 20 - участок визуального контроля;
21 - внешняя граница деталей; 22 - выжигание пустой подвески;
23 - участок сборки; 24 - поднятый участок накопления запаса перед разгрузкой (косая ориентация);
25, 26, 27- участки разгрузки
Поскольку конструкция свободно-приводного конвейера приспособлена к изменениям высоты при движении в вертикальной плоскости, возможна обработка и/или хранение запаса деталей в приподнятом положении. Это, в свою очередь, может увеличить полезную площадь пола, используемую для других целей. Свободно-приводная система пригодна как для перемещения сотен деталей в час, так и для обслуживания малых объемов производства.
Свободно-приводные конвейеры требуют автоматизации. Например, для работы почти всех таких конвейеров необходимы программируемые логические контроллеры (ПЛК). Кроме того, для управления этими автоматизированными конвейерами могут использоваться любые методы взаимодействия с операторами. Наконец, транспортеры для изделий могут оснащаться устройствами кодовой идентификации, от простых механических и инфракрасных меток до оптически считываемых штрих-кодов. Благодаря гибкости свободно-приводных конвейеров кодовая идентификация используется, например, для автоматического направления транспортеров с деталями на конкретные участки загрузки, предварительной обработки, нанесения порошка, нанесения альтернативных или дополнительных покрытий, термообработки, обжига подвесок и т. д. Деталь может пропускаться через систему окраски в соответствии с командами оператора. Базы данных служат также для автоматизации составления технологических маршрутов. Свободно-приводной конвейер может быть легко приспособлен для работы с большей частью автоматического оборудования, включая, роботы-погрузчики и разгрузчики, полуавтоматическое оборудование для загрузки и выгрузки деталей, оборудование для шагового перемещения и перемещения по наклонному квадрату и т. д. Это достигается благодаря способности таких конвейеров перемещать отдельные транспортеры, в то время как оставшаяся часть конвейерной системы продолжает перемещать транспортеры с деталями. Такие транспортеры можно отсоединять от приводной цепи и совмещать с другими транспортерами, что дает возможность организовывать участки для хранения деталей, например, между участками технологических процессов.
Однако свободно-приводной конвейер имеет и некоторые недостатки. Каждая такая установка проектируется по отдельному заказу. Поскольку проектирование такого конвейера требует специального опыта, время, затрачиваемое на проектирование, изготовление и монтаж, будет больше, чем для других систем транспортировки материалов. Кроме того, приходится оплачивать проектирование и сложность; первоначальные капиталовложения в данном случае будут выше, чем для любого другого типа конвейеров. Их использование обычно может обеспечить выгоду и быть экономически оправданным в тех случаях, когда это недостижимо иным способом. Свободно-приводные конвейеры предъявляют также повышенные требования к обслуживанию. Это опять-таки связано со сложностью конвейера и высоким возможным уровнем автоматизации.
8.4. Напольные конвейеры
Ленточные напольные конвейеры
Ленточные напольные конвейеры редко используются для транспортировки деталей в производстве покрытий. В отличие от конвейеров подвесного типа, ленточный конвейер является приспособлением, транспортирующим детали на своей поверхности. Ленточные конвейеры могут транспортировать разные по профилю детали весом от 0,5 кг и меньше до десятков килограммов. Конвейер состоит из пластмассовой ленты или проволочной сетки определенной ширины и приводного устройства. Эта лента движется между двумя боковыми рамами, как показано на рис. 8.11.
На ленточных конвейерах могут использоваться ленты разных типов и разной ширины. Конструкция некоторых лент даже предусматривает возможность поворотов в горизонтальной плоскости и небольших наклонов. На ленточных конвейерах происходит непрерывная обработка изделий без их остановки или накопления.
Ленточная конвейерная система может состоять из нескольких секций. Деление ленточного конвейера на секции или зоны предусматривается для сведения к минимуму влияния различных процессов на конкретную ленту, например для того, чтобы одна и та же лента не переносила детали через печь термообработки и через установку нанесения порошка. Эти секции могут даже двигаться с различной скоростью, как показано на рис. 8.12.
Рис. 8.11. Ленточный конвейер:
1 - проволочная сетка или пластмассовая лента; 2 - боковые рамы; 3 - свободно вращающийся шкив;
4 - ширина конвейерной ленты; 5 - ведущий шкив
Рис. 8.12. Типовая схема движения ленточного конвейера (вид сверху).
Ленточная конвейерная система способна транспортировать детали малого или умеренного веса при малых или средних объемах производства.
Ленточный конвейер имеет ряд достоинств. Монтаж его прост и, следовательно, недорог; такой конвейер просто присоединяется к полу анкерным креплением. Ленточный конвейер удобен при жестком ограничении высоты помещения или в тех случаях, когда транспортировка деталей иным методом была бы затруднительной. Конвейер такого типа обычно используется в системах нанесения покрытий на плоские изделия (заготовки). Ленточный конвейер легко переставлять с одного места на другое, в его конструкцию легко вносить изменения. В отличие от других систем транспортировки материалов, ленточный конвейер может быть полностью собран и испытан вне участка, на котором он будет эксплуатироваться. Наконец, ленточный конвейер легко объединяется с существующей системой конвейеров на участках изготовления, сборки или распределения. При этом, однако, может потребоваться переносить детали с одного конвейера на другой вручную или автоматически.
В то же время ленточные конвейеры имеют многие недостатки и ограничения. В отличие от подвесных конвейеров, ленточный занимает большую площадь пола производственного помещения и постоянно перекрывает проходы. Компоновка ленточного конвейера обычно сводится к прямой линии в пределах системы нанесения покрытий. Оборудование для нанесения покрытий приходится конструировать с достаточным запасом по ширине. Кроме того, существует опасность контакта персонала с открытой движущейся цепью или лентой.
Ленточные конвейеры обеспечивают нанесение покрытия только на верхние, открытые поверхности; нанесение порошка на нижние поверхности детали, соприкасающиеся с лентой, не представляется возможным. В целом существует большая опасность повреждения покрытий по сравнению с другими методами транспортировки. Краска накапливается на поверхности лент, потребность в очистке конвейера и уходе за ним увеличивается. Ленты, проходящие через моечный участок или печь термообработки, обычно выполняются из нержавеющей стали, что делает их более дорогостоящими.
Напольный конвейер с цепью
Другим типом напольного конвейера, используемого в системах нанесения покрытий, является конвейер с цепью. Конвейер такого типа наилучшим образом подходит для обработки больших объемов мелких и легких деталей одинаковой и примерно правильной формы. Он состоит из роликовой цепи с увеличенным шагом (рис. 8.13). Шаг этих цепей составляет обычно от 2,5 до 7,5 см. Цепи перемещаются в специально изготовленной направляющей дорожке. Фиксаторы деталей обычно имеют направляющие и могут иметь встроенное колесо типа шкива для автоматического поворота детали вокруг вертикальной оси.
Область применения конвейеров с цепями ограничивается транспортировкой деталей малых размеров, которые могут автоматически загружаться на шпиндельные фиксирующие приспособления и выгружаться с них при нормальной работе конвейера. Вес детали обычно бывает менее 10 кг.
Конвейер с цепью может иметь крайне малый радиус поворота в горизонтальной плоскости (рис. 8.14). Однако изменение высоты, а также переключение дорожек при использовании конвейера такого типа не представляется возможным. Отдельные детали не могут останавливаться по той причине, что конвейер может либо весь двигаться, либо полностью останавливаться.
Поскольку все детали транспортируются одной конвейерной цепью, все технологические процессы осуществляются с одной и той же скоростью. Конвейерная система с цепью, проходящей по краю, лучше всего подходит для средних или больших объемов производства при окрашивании мелких и легких деталей.
Основной особенностью таких конвейеров является способность работать на большой скорости. Они хорошо сочетаются с простыми роботами, осуществляющими подъем и опускание деталей, т. е. их загрузку и выгрузку.
Рис. 8.13. Напольный конвейер с цепью:
1 - шкив поворотного шпинделя; 2 - фиксирующее приспособление;
3 - секция направляющей дорожки; 4 - конвейерная цепь
Рис. 8.14. Типовой транспортный путь напольного
конвейера с цепью (вид сверху):
1 - выгрузка; 2 - робот для подъема и опускания деталей; 3 - загрузка;
4 - печь для отверждения покрытия; 5 - поворот детали в процессе нанесения порошка;
6 - камера для нанесения порошка; 7 - помещение для нанесения покрытия;
8 - агрегат для подготовки поверхности; 9- сушильная камера
Детали, требующие нанесения покрытия только на внешние поверхности являются идеальными для конвейеров такого типа, поскольку в этом случае деталь закрепляется снизу и по центру. Кроме того, характер фиксации детали на конвейере с цепью, проходящей по краю, является идеальны для поворота деталей вокруг вертикальной оси. Такой поворот может действительно потребоваться в процессе нанесения покрытия. Цепи, проходящие по краю, допускают в горизонтальной плоскости повороты предельно малого радиуса, что дает возможность делать участки более компактными. Блок управления требуется простейший.
В таких системах невозможно переключать маршрут движения деталей или обрабатывать их при различных скоростях. Как и другие напольные конвейеры, конвейер с цепью занимает большую площадь пола производственного помещения и постоянно перекрывает проходы. Кроме того, существует опасность контакта персонала, присутствующего на участке, движущимися изделиями.
8.5. Выбор транспортных средств
Транспортное оборудование выбирают и рассчитывают в соответствии с принятым и разработанным технологическим процессом окрашивания с учетом многих факторов.
В случае поточных производств при выборе конвейера требуется, как минимум, следующая информация:
- характер помещения для монтажа, желаемая компоновка, инженерное обеспечение и т. д.;
- полная характеристика окрашиваемых деталей;
- характер проводимых видов работ и их продолжительность;
- объем производства и принятый режим работы цеха.
Информация, касающаяся помещения, в котором будет монтироваться
конвейер, требуется для определения трассы движения конвейера и общей компоновки. Она должна включать чертежи производственных площадей и оборудования с указанием линии колонн и высоты помещения. Полезна информация о расположении вентиляционных шахт, пожарных гидрантов и инженерных сетей.
Для правильного выбора конструкции конвейера должна быть предоставлена также полная информация о деталях, которые будут транспортироваться. Необходимо знать максимальную высоту, ширину, длину и массу для каждого типа деталей. При определении размеров деталей следует уделить особое внимание их ориентации. Такие данные важны для проектирования участков очистки поверхности, промывки и нанесения покрытия.
При выборе конвейера должны учитываться не только максимальные размеры отдельно взятой детали, а параметры (например, максимальное поперечное сечение) группы деталей, комплектующихся на одной подвеске.
Поэтому необходимы данные:
- о максимальной высоте, ширине и длине комплекта деталей на подвеске;
- количестве этих деталей;
- максимальной их массе.
Эти требования используются для определения пропускной способности конвейера и рабочих скоростей.
При расчете подвесных конвейеров необходимо также учесть просвет между нижней частью дорожки и верхней частью детали. Это расстояние, которое обычно называют просветом конвейера, зависит от типа подвесного конвейера и от метода подвески деталей. Здесь возникают две основные проблемы. Одна из них в том, что детали, двигаясь по кривым в вертикальной плоскости, ни за что не должны задевать (рис. 8.15 и 8.16), а другая - обеспечить, чтобы ни одна из несъемных частей конвейера (дорожка, цепь, тележки, санитарные S-образные крюки и нагрузочные рычаги) не покрывалась порошком. Просвет конвейера при одноточечном и двухточечном подвешивании деталей может быть различным.
При рассмотрении ориентации и веса деталей следует оценить их теплоемкость в связи с необходимостью нагрева, сушки и термообработки. Следует обратить особое внимание на значительные колебания массы. Большие различия в массе могут потребовать специальных методов для обеспечения многократных циклов термообработки. В действительности это возможно только при использовании ручных конвейеров типа "тяни-толкай" или свободно-приводных конвейеров.
Помимо технических условий на детали, определяющих их размеры и вес, требуются также данные о скорости обработки деталей (количество деталей в час). Эти величины должны характеризовать наихудший случай работы при существующих уровнях производства и запас на дальнейшее увеличение производства, насколько это применимо. Они являются основой для определения чистой производительности. Для непрерывно движущихся конвейеров чистая производительность приравнивается к линейной скорости системы. Подвесные конвейеры высокой пропускной способности могут двигаться со скоростью порядка 0,25-0,3 м/с.
Рис. 8.15. Положение деталей при подъёме конвейера
(одноточечная подвеска деталей, вид сбоку):
1 — нижний уровень; 2 - просвет конвейера;
3 - расстояние между обрабатываемыми деталями;
4 - радиус вертикальной кривой; 5 - подвесной конвейер;
6 - верхний уровень;
7 - просвет между внешними границами деталей; 8 - внешняя граница деталей максимальных размеров
Для систем с ручными транспортерами чистая производительность выражается числом единиц, проходящих за 1 ч. Пропускная способность ручных систем обычно составляет всего несколько единиц. Необходимые размеры просветов между деталями и конвейерами должны быть выверены для обеспечения свободного прохождения деталей как по кривым в вертикальной плоскости при изменении высоты (см. рис. 8.15 и 8.16), так и при горизонтальных поворотах (рис. 8.17 и 8.18). Необходимые просветы должны быть учтены при расчетах производительности системы. Эти расчеты должны быть подкреплены чертежами. Затем полученные значения вводятся в технические условия на конвейер.
Рис. 8.16. Положение деталей при подъёме конвейера
(двухточечная подвеска деталей, вид сбоку):
1 - нижний уровень; 2 - подвесной конвейер; 3 - расстояние между обрабатываемыми деталями;
4 - радиус вертикальной кривой; 5 - просвет конвейера; 6- верхний уровень;
7- просвет конвейера в кривой; 8 - внешняя граница деталей максимальных размеров;
9 - просвет между внешними границами деталей
На большинство проектов окрасочных линий налагаются жесткие ограничения в отношении капиталовложений, необходимых для их реализации. Системы транспортировки - непременные элементы установок для нанесения покрытий. Выбор прогрессивного метода транспортировки изделий и соответствующего оборудования может повысить эффективность и рентабельность всего производственного процесса. Важно понять, что использование новаторских решений в транспортировке материалов и изделий может повысить прибыль, получаемую с инвестированного капитала. Более быстрая окупаемость может быть реализована за счет снижения незавершенного производства, обеспечения оперативной поставки узлов,
Рис. 8.17. Положение деталей при горизонтальном повороте конвейера
(одноточечная подвеска деталей, вид сверху):
1 - внешняя граница деталей максимальных размеров; 2 - внешняя граница детали при вращении;
3 - средняя линия подвесного конвейера; 4 - расстояние между обрабатываемыми деталями;
5 - просвет между внешними границами деталей; 6 - радиус горизонтального поворота
Рис. 8.18. Положение деталей при горизонтальном повороте конвейера
(двухточечная подвеска деталей, вид сверху):
1 - максимальное расстояние между точками подвески;
2 - просвет между внешними границами деталей;
3 - расстояние между обрабатываемыми деталями; 4 - средняя линия подвесного конвейера;
5 - внешняя граница деталей максимальных размеров;
6 - радиус поворота (в горизонтальной плоскости)
снижения или устранения необходимости в ручных перемещениях грузов в процессе работы и улучшения эргономических условий, связанных с транспортировкой деталей через участки технологической цепочки.
8.6. Эксплуатация и техническое обслуживание конвейеров
Как только ключевые вопросы, такие, как размещение, маршрут перемещения, тип конвейера и производительность технологического процесса, будут решены, необходимо оценить некоторые другие составные части проекта.
Рассмотрим основные положения, связанные с эксплуатацией конвейеров. Заслуживают внимания следующие вопросы:
- работа узла привода;
- нагрузка на цепь и ее длина;
- подтягивание цепи;
- изменение высоты;
- опорные конструкции;
- защитные ограждения;
- системы смазки;
- системы очистки;
- методы заземления;
- контроль производительности;
- требования безопасности;
- методы и варианты управления.
Узел привода - элемент всех конвейерных систем. Это механическое устройство, которое с помощью своего электродвигателя приводит в движение конвейерную цепь через червячный или зубчатый передаточные механизмы. Узлы привода с подвижной рамой, которая позволяет двигателю, редуктору и передаточному механизму перемещаться, обычно считаются более предпочтительными по сравнению с узлами привода, в которых используются неподвижные рамы.
Узел привода располагают таким образом, чтобы тяговое усилие прилагалось к секции конвейера с максимальной нагрузкой. Он часто монтируется в местах подъема. Поскольку узлы привода имеют множество движущихся частей и должны смазываться, необходимо, чтобы к ним имелся легкий доступ для обслуживания. Кроме того, узел привода может быть расположен перед моечным агрегатом или между участками загрузки и выгрузки, где присутствует только пустая цепь. Размеры узла привода выбирают на основании максимального расчетного тягового усилия цепи.
Тяговое усилие цепи характеризует то усилие, которое необходимо для обеспечения движения цепи по всей производственной системе. Оно является функцией максимального веса детали, транспортируемой цепью, расстояния между деталями, общей длины цепи, изменений высоты системы. Усилие, создаваемое узлом привода, должно превышать максимальное усилие, которое требуется для движения цепи. Узлы привода могут развивать усилие от 40 до 1400 Н и более, в зависимости от типа и размеров транспортируемых изделий. В некоторых случаях для длинных цепей или больших нагрузок может потребоваться более одного узла привода. В таком случае используется контрольная система распределения тягового усилия между этими узлами привода.
При движении цепей, имеющих большую длину, множество горизонтальных поворотов, изменений высоты, подверженных резким изменениям нагрузки от смешанных деталей или при неудовлетворительной смазке, могут возникать колебания скорости и толчки. Поскольку такие явления могут привести к образованию дефектов покрытия, конвейер следует конструировать таким образом, чтобы устранить или свести к минимуму колебания скорости и толчки в движении цепи в системе нанесения покрытий.
Для каждой замкнутой конвейерной линии требуется устройство для поддержания натяжения цепи, необходимого для оптимальной производительности. Подтягивание цепи необходимо при провисании цепи. Ослабление или провисание цепи может быть вызвано движением деталей вниз при изменении высоты, неравномерной загрузкой цепи или растяжением в результате продолжительного использования. Устройства натяжения цепей бывают следующих типов:
- противовес;
- пружина;
- винт;
- пневматические или гидравлические устройства.
Устройства натяжения цепи следует всегда располагать после узла привода, в непосредственной близости от него.
Во многих случаях требуется, чтобы детали находились на разной выоте при прохождении различных участков производственного процесса. Гибкость, которую обеспечивают конвейерные системы с изменениями высоты, позволяет разместить узлы для загрузки и выгрузки деталей на оптимальной высоте. Детали могут проходить через агрегат подготовки поверхности, камеру нанесения порошка или печь на высоте, желательной для пользователя. Для конвейерных систем с непрерывным движением цепи и свободно-приводных конвейеров эти изменения высоты осуществляются по криволинейным участкам дорожек конвейеров в вертикальной плоскости (см. рис. 8.16). Возможность скольжения деталей при прохождении ленточного конвейера по наклонным участкам нужно обязательно исключить.
Другим средством транспортировки деталей при изменении высоты на ручных или свободно-приводных системах является использование тали. Таль может вертикально поднимать и опускать деталь в установленном месте. В системах транспортировки деталей с непрерывным движением цепи не могут использоваться механизмы подъема/опускания, поскольку деталь поддерживается на непрерывно движущейся конвейерной цепи.
Любой конвейер должен поддерживаться соответствующей опорной конструкцией. Ленточный или цепной конвейер обычно просто присоединяется анкерным креплением к полу производственного помещения или технологическому оборудованию. Различные подвесные конвейеры могут поддерживаться потолочными стальными конструкциями, либо стальными колоннами, поднимающимися с пола, либо комбинацией этих конструкций. Любые потолочные опорные конструкции должны быть прикреплены к стальному каркасу здания.
Для обеспечения безопасности персонала вокруг подвесного конвейера рекомендуется иметь защитное ограждение. Оно требуется в тех случаях, когда просвет под ограждением составляет не менее 2 м. Ограждение служит для защиты персонала, находящегося под конвейером, от падения деталей или крюков, которые могут сорваться с подвесного конвейера.
Ограждение может выполняться из проволочной сетки, сетки из прутьев или листового металла, в зависимости от размеров и массы деталей. Размеры защитного ограждения должны выбираться таким образом, чтобы детали самых больших размеров, свешивающиеся с конвейера, проходили над ограждением с достаточным просветом, включая места горизонтальных поворотов и изменений высоты, с учетом возможного раскачивания и вращения деталей.
Каждый тип конвейерных систем требует смазки для обеспечения нормального функционирования. Недостаток смазки уменьшает срок службы, приводит к неустойчивой работе конвейера, увеличивает необходимое тяговое усилие для движения цепи и вероятность остановки вследствие преждевременного выхода из строя тех или иных частей конвейера.
Ручные конвейеры требуют смазки только тележек и переключателей дорожек. Ленточный конвейер нуждается в смазке подшипников. В конвейерах с непрерывным движением цепи и свободно-приводных смазывают цепи, все движущиеся части, включая соединительные звенья и подшипники. Смазка особенно важна для тех цепей, которые должны переносить детали через моечные участки и печи. Естественно, в каждом конвейере кроме компонентов механизма, несущих нагрузку, в смазке нуждаются редуктор или коробка передач.
В тех случаях, когда конвейер проходит через печь, нужна высокотемпературная консистентная смазка, выбирать ее следует с особой тщательностью. Цепи подвесных конвейеров должны поставляться с масленкой или устройством автоматической смазки. Автоматические масленки наиболее предпочтительны для установок, которые работают строго по таймеру.
Правильно выбранный смазочный материал должен:
- обеспечивать снижение трения и потребления энергии;
- проникать в труднодоступные места и растекаться по поверхностям;
- предотвращать истирание поверхностей;
- предотвращать зацепления;
- предотвращать коррозию;
- выдерживать высокую рабочую температуру и температуру окружающей среды;
- не притягивать пыль и другие истирающие материалы;
- обеспечивать легкость нанесения, которая позволит точно контролировать количество смазочного материала.
Для цепей многих подвесных конвейеров используются некоторые типы жидких смазочных материалов, не высыхающих или высыхающих с образованием твердой пленки, в которых используется дисульфид молибдена или другой материал молибденового типа, наносимый автоматическим устройством. Высыхающие смазки особенно распространены в технологии нанесения покрытий. Состав этих материалов обычно подбирается таким образом, чтобы они содержали не только вещества, снижающие трение, но и смачивающие и смазывающие добавки, а также ингибиторы коррозии. Смазочные материалы в виде сухой тонкой пленки позволяют удалять любые загрязнения с несущих поверхностей конвейера. Смазывающей жидкостью покрывают поверхность (цепи и др.). Она проникает в узкие щели, растекаясь по металлу, и после улетучивания растворителя оставляет тонкую пленку твердого смазочного материала с дисульфидом молибдена.
Этот материал хорошо связывается с микроскопическими неровностями поверхности металла. Образующаяся сухая скользкая пленка способна выдерживать давление до 6800 атм. По мере нарастания сухой пленки несущие поверхности принимают металлический оттенок или блеск. По сравнению с описанными материалами смазочные материалы на жидкой основе не распространены в технологии нанесения покрытий. Они имеют тенденцию к притягиванию пыли и порошка и являются потенциальным источником загрязнения покрытий при отсутствии точного контроля. Нельзя применять смазки на основе силиконов. Они могут отрицательно повлиять на качество покрытий, хотя конвейерные цепи, смазанные ими, могут легко и непрерывно работать при повышенных температурах около 150-200 °С.
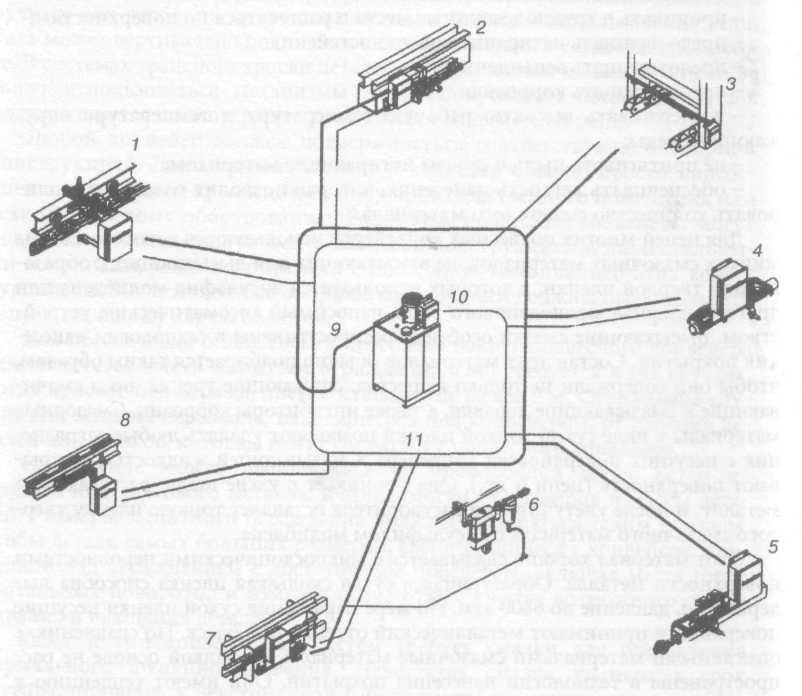
Рис. 8.19. Централизованная система подачи смазочного материала:
1 — монорельс; 2 - обратный привод; 3 - двойная ветвь;
4 - трубчатый узел; 5 - закрытая дорожка; 6 — свободный транспортер с обратным приводом;
7 - инвертированный конвейер; 8 — траншейный узел; 9 - линия смазочного материала;
10 — линия подачи электрического питания;
11 — центральная система смазки с емкостью на 200 л
Существует два основных метода нанесения смазочного материала на рабочие и движущиеся конвейерные цепи, а также подшипники тележек. Первый и наиболее часто используемый метод заключается в подаче смазочного материала растворного типа в точно контролируемых количествах в подшипники, точки износа и на поверхности, требующие смазки (рис. 8.19). Второй метод применяется для конвейеров с герметичными подшипниками. Их смазывают консистентной смазкой вручную или автоматически.
Конвейерная система, проходящая через все стадии процесса нанесения покрытия, может загрязняться, что вызывает необходимость ее периодической чистки. С этой целью применяют щеточные очистители. Они предусмотрены для очистки конвейерных цепей, тележек, дорожек и санитарных крюков.
Рис. 8.20. Типичные щеточные очистители конвейеров:
а — закрепление немеханизированного щеточного очистителя на цепи для секций закрытой дорожки;
б - то же для цепи и колес закрытой дорожки; в - механизированный
и г - немеханизированный щеточный очиститель для цепи и тележек двутавровой балки
Щеточные очистители конвейеров могут быть механизированными либо немеханизированными. В механизированных очистителях, монтируемых на дорожке конвейера, обычно используются круглые щетки из проволоки или жесткой пластмассы. Механизированные щеточные очистители могут иметь микропроцессорное управление, так что время и продолжительность очистки могут быть запрограммированы. Все механизированные щетки должны иметь ограждение для сведения к минимуму разбрасывания удаляемых загрязнений и пыли (рис. 8.20).
Немеханизированные щеточные очистители могут быть неподвижными, используемыми для очистки движущейся конвейерной цепи, или прикрепленными к движущемуся конвейеру для очистки поверхностей дорожки конвейера, несущих нагрузку, как это показано на рис. 8.20. Немеханизированные очистители конвейерной цепи и тележек монтируются на дорожке конвейера таким образом, что их щетки приводятся в соприкосновение с различными участками движущейся конвейерной цепи. При движении конвейера щетки вращаются. Усилие, прилагаемое к немеханизированному очистителю конвейера, обычно регулируется пружинами или фрикционной муфтой. Немеханизированные очистители дорожек закрепляются на конвейерных цепях. После прохождения нескольких циклов конвейерной системы их снимают.
Детали, транспортируемые конвейерной системой, должны быть надлежащим образом заземлены. Используется несколько видов заземления. Обычно на рельс конвейера устанавливают медные щетки или приспособления в виде подвижных стержней. Проходя мимо них, подвески деталей соприкасаются со щетками, обеспечивая их соединение с землей.
Другим местом заземления является точка контакта детали с подвеской. Часто пытаются создать универсальное приспособление для подвески, которое обеспечивало бы большую гибкость и меньшую стоимость транспортировки и производства. Но при этом точки контакта детали с приспособлением для подвески, открытые во время нанесения, обрастают порошком и изолируются. Более рациональна конструкция приспособления для подвески с использованием ножевого контакта. В данном методе, как показано на рис. 8.21, приспособление для подвески имеет острую грань в месте соприкосновения с деталью. В процессе транспортировки порошок ссыпается с острия, обнажая контакт. Чем больше нагрузка от детали на приспособление для подвески, тем меньше проблем с заземлением в данной контактной точке, поскольку острая грань легче проходит через слой порошкового материала.
Следующий контактный участок - точка контакта приспособления для подвески с нагрузочным рычагом, транспортером или тележкой. Это соединение не проходит через камеру нанесения порошка, так что вероятность оседания на нем порошка ничтожно мала. И все же полезно учитывать требования проводимости в данных точках путем сведения к минимуму контактов двух плоских поверхностей и применения вместо этого ножевых контактов, где это возможно.
Рис. 8.21. Ножевой (или точечный ) контакт подвески с деталью
(увеличенный вид сбоку в точке подвески детали):
1 - точка контакта; 2 - отверстие для подвески;
3 - деталь; 4 - приспособление для подвески детали
Приспособления для подвески деталей должны часто очищаться для удаления осевшего непроводящего порошка. Крюки, на которые подвешиваются детали, требуют очистки, по крайней мере, один раз в день. В случае нанесения жидких красок для очистки крюки полностью опускают в раствор каустической соды, а в случае порошковых материалов, как правило, используют высокотемпературную печь для выжигания с последующей промывкой водяной струей.
Наконец, нужно отметить, что при избыточной смазке часть ее может попадать в точки контакта, нарушая заземление и приводя к осаждению порошкового материала на детали. Поэтому надлежащая смазка конвейера имеет большое значение для достижения оптимальной производительности конвейера и заземления деталей.
Контроль и обслуживание конвейера осуществляют при постоянном наблюдении, однако существуют вспомогательные средства, облегчающие контроль производительности конвейера и его эксплуатационных характеристик.
Имеется возможность полуавтоматического контроля с помощью системы управления или компьютера. Система управления может сигнализировать о любых ситуациях в ходе работы конвейера, которые являются или могут стать факторами, определяющими производительность конвейера или его потребность в техническом обслуживании. Примером может служить остановка конвейера при отсутствии смазочного материала в резервуаре системы смазки. Другие параметры работы конвейера, которые необходимо контролировать:
- скорость конвейера;
- температура конвейерной цепи;
- показания амперметра двигателя привода;
- растяжение цепи;
- давление в системе подтягивания цепи (при использовании пневматической или гидравлической системы);
- температура редуктора или коробки передач узла привода;
- температура задней стенки или направляющей узла привода;
- работа системы смазки;
- работа щеточных очистителей
Получив сигнал об отклонениях от нормального функционирования или неисправности в работе конвейера, можно принять меры по их устранению без дорогостоящего простоя, вызванного износом или отказом отдельных частей.
8.7. Безопасность и методы управления
Требования безопасности
Безопасность персонала при эксплуатации и обслуживании конвейера является первоочередным требованием. Во всех местах, где это возможно, должны использоваться защитные ограждения, все движущиеся части конвейера должны быть закрыты и защищены. В местах изменения высоты в системах с непрерывным движением цепи и свободно-приводных системах могут быть предусмотрены приспособления, препятствующие сходу деталей с конвейера, их откату назад или потере в случае обрыва цепи.
Все механизмы секции подъема и опускания должны иметь блокировочные механизмы для закрепления тележек на таких секциях до их подъема или опускания. Все узлы привода конвейеров должны быть оборудованы устройствами защиты от электрических и механических перегрузок, и должна быть обеспечена возможность немедленной остановки конвейера. Для персонала на опасных участках должны находиться соответствующие предупреждающие таблички, цепные ограждения и использоваться полосатая окраска. Должна быть предусмотрена подача звукового сигнала перед включением узла привода конвейера.
На всех участках системы должны быть предусмотрены устройства экстренной остановки, чтобы операторы могли быстро остановить конвейер в аварийной ситуации. Все панели управления и узлы привода должны иметь блокировочные приспособления для предотвращения включения конвейера при выполнении технического обслуживания. Эти приспособления должны полностью исключать возможность работы конвейерной системы с отключением электрического питания. Наконец, надлежащее техническое обслуживание и визуальный контроль в сочетании с необходимым обучением операторов являются непременными условиями безопасной эксплуатации любого промышленного оборудования, в том числе такого, как конвейерная система.
Методы и варианты управления
Для управления конвейерной системой на участках нанесения покрытий может быть выбрано множество методов и вариантов. Ручные системы типа "тяни-толкай" не требуют никаких систем управления. Большинство органов управления ими приводится в действие вручную. При необходимости может быть использовано простое реле или пневматическое логическое устройство, которые могут помочь пользователю такой системы переключать дорожки или другие устройства.
Системы с непрерывным движением цепи могут иметь блок управления для установки регулируемой скорости привода, а также индикатор скорости. В большинстве конвейерных систем с непрерывным движением ленты используются простые системы управления на основе реле. В системе управления любого механизированного конвейера должны предусматриваться подача предупредительного сигнала перед его включением, возможность экстренной остановки и остановки при перегрузке.
Практически во всех свободно-приводных конвейерах используются программируемые логические контроллеры (ПЛК). Такие контроллеры, используемые в сочетании с другими приборами (механический или инфракрасный идентификатор, штрих-код и т. д.), могут быть сконструированы для автоматического подбора, обработки, сортировки и отправки детали по заданному маршруту. Система управления на основе программируемого логического контроллера может быть также объединена с программами составления технологических маршрутов или управления предприятием. Программируемые логические контроллеры могут использоваться для контроля качества с использованием таких методов, как слежение в процессе выполнения работ или статистический контроль технологического процесса.
Поскольку существует много различных систем управления, известно также много различных методов связи операторов с управляемыми системами. Простейшим операторским интерфейсом является использование контрольных ламп на панели управления для индикации конкретных ситуаций. Основные органы управления системой могут быть приведены в действие простыми кнопками или переключателями на панели управления.
Следующим уровнем сложности является цифровой дисплей, заменяющий индикаторные лампы или используемый в сочетании с ними. Цифровые дисплеи выдают более подробные сообщения о состоянии системы. Еще более высоким уровнем операторского интерфейса является графический интерфейс пользователя. Вся система управления может приводиться в действие и контролироваться с графического дисплейного терминала. Графический дисплейный терминал может представлять собой маленький монохроматический экран с функциональными клавишами или цветной сенсорный экран промышленного персонального компьютера. Графические интерфейсы пользователя могут быть использованы для иллюстрации критических параметров технологического процесса (температуры на этапе промывки, температуры печей, числа подвесок с деталями, прошедших через участки обработки, и т. д.).
В конвейерной системе может применяться много способов оповещения о состоянии системы. Для оповещения всех операторов на участке о предстоящем включении и других условиях работы обычно используются звуковые сигналы. Другими средствами оповещения могут быть сигнальные огни, стробоскопические источники света или цветные лампы.